Back in 2004, the steel industry was demanding new advances in technology. Italian machinery provider Ficep decided to adapt its fast beam-drilling machines with milling capabilities. This allowed progressive manufacturing companies to scribe on a steel beam all information that was needed to automatically fit the beam to the production process of a whole assembly.
"In 2004, when the steel market was practically demanding new technology as a must-have, we were pushed to launch a new revolutionary solution," says Christian Colombo of Italian machinery supplier Ficep. "Given the fact that drilling had become so fast with new carbide and hard-steel tools, there were possibilities to use this technology even further."
Visionary fabricators' push forward
"We enhanced the computer-numeric control (CNC) capability of drilling by using contouring from the thermal cutting machines that we had already developed and proven," Colombo continues, "and combined it with a request from our visionary customer Mueller Inc.From Texas. We decided to adapt our beam drilling machines with milling capabilities in order to allow Mueller to scribe on a beam all the fit-up information that was going to be manually added downstream in the production process."
We have applied for patents regarding scribing innovation internationally, for the process of automatic manufacture and marking-out of multiple component objects as well as for the engraving and marking device for machine tools with which to do it," says Colombo. "In some countries the patent has already been approved."
What is scribing?
Scribing is the process of collecting information from a computer model and then automatically transferring it by marking the locations and part marks to the main piece of a stee assembly. This automatic process reduces laborious fitting processes and ultimately reduces human error through improved automation, changing the traditional way of making steel assemblies. The method expands the realm of CNC automation from just punching, drilling, cutting, and coping to also include layout and fitting, the most expensive shop fabrication operations. With new, automatic scribing tools, information is read directly from the 3D model allowing shop fitters to see exactly which detailed material to place and where on the main member. All new drilling lines manufactured by Ficep are compatible with this technology, like ficep beamline.
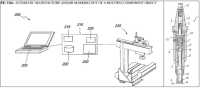
Elements of scribing innovation that the patents have been applied
Idea of automatic layout marks
How did it all begin? Let's hear Rayome Soupisetof Mueller Inc, Texas, the main man behind the innovation, tell the story.
"The major reason to drive the idea of automatic steel layout marks was to eliminate human error,"Soupiset says. "We started searching to place CNC-controlled layout marks onto structural steel used for metal buildings to eliminate human error."
"Consistency was the next major issue, regardless as to whether the marks were 'correct' or not," Soupiset continues. "This means that if at Mueller we could place a clip, gusset, stiffener, connection plate, or wind bent, where we wanted them to be in a steel assembly, if an error was later found in the design or detailing of the steel parts, we as the fabricator would know what parts had to be corrected."
For cost savings and better working conditions
"With the automatic layout marks, we also seeked to eliminate field-back charges," Soupiset says. "Erectors and contractors would back-charge Mueller for correcting our errors in the field. They would charge for lost man-hours, machinery and profits incurred for the time it would take to correct the issue."
"Another thing was to improve working conditions for the men and women doing the work in the steel shop. In the past it would require 4 to 8 knowledgeable, qualified workers to mark 200 parts per day, working 10 to 12 hours, 5 to 6 days a week, in temperatures in excess of 100 degrees. With a CNCcontrolled machine doing layout marks—as well as cutting to length, cutting to angle, and drilling holes—one operator could run multiple machines with less physical effort and achieve better and more reliable results in less time."
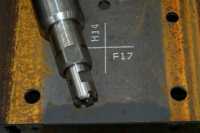
Ficep milling tool and fit up marking
Slow steps to find a vendor
So, how was this idea developed further? "Slowly and painfully would be the most honest and direct answer," Soupiset gives a laugh. "It started out as a conceptual idea between the owner of Mueller, Bryan Davenport, and myself as the operation officer. Once the concept was approved and research and development funds appropriate, we went looking for a vendor." "We went to many CNC machine manufacturing companies. No one wanted to take the project on for us. Then we asked a company named Metalforming, located in Peachtree City, Georgia. They said it was beyond their ability but recommended Ficep. Their owner Geoffrey Stone had had conversations with Christian Colombo of Ficep. This was the catalyst that started everything."
Ficep beamline picks up the gauntlet
"Mueller contacted Ficep USA and arranged a visit," explains Rayome Soupiset. "When we introduced our idea, they wanted to double-pass the steel beam, rotating it after one pass, to mark the fourth side of the beam. This was unacceptable to Mueller as it would have doubled our production times."
"I flew to Italy with Jon Kahrl, from Ficep’s representative in Texas, Capital Machine Technologies, to speak with Ficep, and met with Christian Colombo. Half way through a plant tour, I saw a pneumatic drill on another piece of equipment and asked Christian why he could not apply that drill to the bottom side of a drill line to be used as a scribing tool, to achieve marking all four sides of the beam in one pass on the line. Christian stopped, thought for a minute, and said that yes, Ficep could do that."
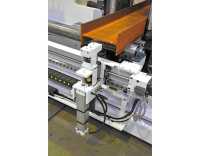
Underside scribing
Mueller gets enough and more
"Once a price for the development was quickly settled, we had a deal with Ficep," Soupiset recalls. "This was the start of scribing a steel beam, on all four sides, as well as cutting to length, cutting to angle, and drilling holes, in a single pass."
"We came away with marking on four sides of the steel beam, cutting to length, cutting to angle, drilling holes and slots, optimizing beam usage, doing automated issues from the CNC controller of the beam line via Steel Projects software and printing a drawing after the part was cut on the shop floor. Now we have one operator running two beam lines who can do the work of 12 people, faster, safer, and more reliably," he concludes.
Overcoming challenges enables industry development of ficep beamline
"One of the hardest parts of developing automatic layout marking was software integration," Soupiset says. "Mueller had to develop and implement an internal system that went from design to detailing to CNC controlling the Ficep drill beamline, saw and scribe line. This did not exist in the metal building industry before. Based upon guidance from Ficep, we developed layered DXF files that could be used for this purpose."
"The distance between Mueller and Ficep in Italy was another challenge. This machine being the first of its kind in the world and Mueller being located in a rural western part of Texas, the time difference and logistics of understanding one another was tough at times. When Christian and I got together, we joked that smarter men would not have started this project. However, this was noted as an issue up front and was to be expected. Over all everything went well," Soupiset recalls.
"Another client of ours, Barrett Steel Buildings Ltd. Of Bradford, UK, wanted to do the same utilizing intelligent Tekla building information modeling (BIM) interface, which was the most logical step forward for us, too, says Christian Colombo.

Steel assembly in Tekla Structures software
"After years of development, Ficep’s leading edge attracts interest around the world as our competition is obliged to try and emulate what we have achieved," says Colombo. "The solutions that we have been experimenting with for years are benchmarks for the industry. Now that we have the basic solutions available, we will continue the work within Ficep so that we will always be at the forefront of technology throughout the structural steel industry."
-----------------------------------------------------------------------------------------------------------------
Ficep beamline
Headquartered in Varese, Italy, Ficep is the leading manufacturer of machine tools for the steel construction fabrication industry with customers in nearly 90 countries globally. The company provides the world's widest range of machines for both the forging and structural steel industries. Ficep S.p.A. was founded by the family of the present owners in 1930. For over 80 years the company has grown from a manufacturer of manual machines to a leader of the most advanced CNC machine tool technologies in the steel construction industry.
Mueller
Mueller, Inc. has been around for over 75 years. The business began when Walter Mueller opened the Mueller Sheet Metal Company in Ballinger, Texas. Mr. Mueller built the family business by providing quality water cisterns crafted from sheet metal to local farmers and ranchers. Over the years, Walter's sons, Harold and James, expanded the business to include other sheet metal products related to building construction.
In 1984 the Burly Corp., a privately held Texas company owned by the Davenport family, acquired Mueller Supply Company from the Mueller brothers. Since that time Mueller, Inc. has undergone rapid expansion becoming a leading manufacturer of pre-engineered metal building and residential metal roofing products.
Today, Mueller, Inc. serves the Central and Southwest U.S. markets from 28 distribution and 3 manufacturing locations, employing 600 people, while continuing in its heritage of directly serving the end user with quality metal building products.
While maintaining a strong financial base, Mueller is committed to continuing its long-term growth rate through satisfied customers.
To receive updates on the lastest product like ficep beamline gear subscribe to our newsletter, go to: www.ronmack.com.au